Distillation device for the production of cognac, brandy, brandy model "C27 CADALPE"
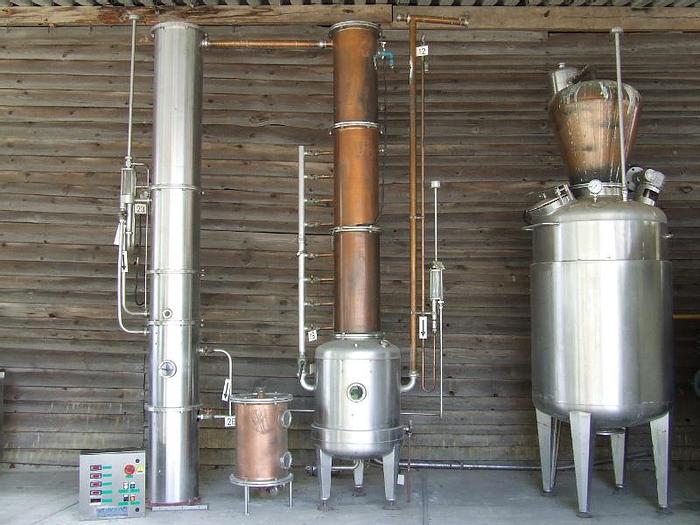
Distillation device for the production of cognac, brandy, brandy model "C27 CADALPE"
Location:Siemyśl, Poland
Description
Distillation device for the production of cognac, brandy, brandy model "C27 CADALPE" Data on the distillation plant: 1. The team consists of: - Distiller (alcohol discharge device - A) made of steel stainless steel and copper with a working capacity of 8-10 l, equipped with slow-speed stirrer driven by a 1.5 HP motoreducer. It has a hatch for loading product, butterfly valve for product discharge, sight glass on top and on disking, connections for probes, jacket for steam heating, connection steam supply, aeration connection with a suitable device draining valve, pressure gauge, condensate discharge connection complete with unloading device. The distiller has a copper dome with a sight glass, and it is equipped with an external separating cyclone made of stainless steel, which separates possible foaming from the steam, it also has a spray ball for washing. In addition is equipped with: cast iron steam regulating valve, two PT 100 probes for measurement temperature. - Device (Filter for neutral substances - B) for absorption that may occur sulfur dioxides, which may appear in alcohol vapors; it is copper a cylindrical tank having flanged ends to match the inert material and equipped with 2 sight glasses, copper pipes with a three-way valve for discharge alcohol vapors and shut-off valve. - Copper enrichment column (Distillation column - C with flow condenser - D) with eight plates, made of copper with a stainless steel boiler and condensate diverter on top. Equipped with 2 sight glasses (one placed on the eighth plate, while the other is placed between the second and third plates), connection of temperature probes, flow meter showing the amount of water flow to the condenser, water condensate control ball valve, condensate circulation pump water, a heating system located at the bottom of the column with a manually controlled valve and unloading device. Each plate is equipped with an unloading valve connected to which can be used to separate the plates and to wash the column. - The vertical column with various connections consists of: - Alcohol vapor condenser (Alcohol vapor condenser - E): copper coil heat exchanger having the appropriate cross-section and surface placed in the stainless steel cylindrical tank with flanged ends and probe connection. - Cooler (Distillate Cooler - F): this is a copper coil heat exchanger having a suitable cross-section and surface located in a stainless steel cylindrical tank with flanged ends and connection probe, placed under the condenser. - Flow meter and ON-OFF solenoid valve: to stop the water needed for the desuperheater and condenser. - Tank for collecting leading (main) portions (Head Fraction Tank - G): cylindrical in shape, made of stainless steel, equipped with a sight glass, solenoid valve for cutting off and discharging the heads, glass tank for cutting off the heads using a volumetric control, creating a structural element of the column placed under the cooler. The tank is designed to receive from the condenser main portions to be extracted. - Tank for collecting final portions (Final fractions tank - H): cylindrical, made of stainless steel, equipped with a sight glass, solenoid valve cutting off the final portions, photocell cutting off the ends by controlling the alcohol content, creates a structural element of the column and is located under the main collection tank. This tank is intended for the final portions, which we decide to separate from "good taste". 2. Specifications: - Amount of raw material treated during 1 cycle - 1,000 l; - Duration of the cycle - from 2.5 to 4.5 hours (depending on the composition and physical characteristics of the raw material); - Maximum share of solids in the distilled liquid - 50%; - The maximum recommended alcohol content in the distilled raw material - 10/12%; - Maximum steam pressure - 0.5 bar; - Steam working pressure - 0.2/0.5 bar; - Permissible pressure when unloading condensate - 0 bar; - Steam consumption during the heating phase - 120/140 kg/h; - Time to reach the temperature in the heating phase from 20 to 93 °C - 0.45/1 h; - Steam consumption during the distillation phase - 50/80 kg/h; - Duration of the distillation phase - 1.5/3 h; - Cooling water consumption (temp. 15 °C) per cycle - 2,000/3,500 l; - Maximum instantaneous flow of cooling water - 2,000 l/h; - Recommended cooling water pressure - 0.5 bar; - Temperature of water leaving the condensers - 60/70 °C; - Washing water consumption per cycle - 80/150 l; - Instant washing water flow - 7,000 l/h; - Washing water pressure - 2/3 bar; - Calcium carbonate input to the reactor filter - 70 kg; - Installed power - 2 kW; - Protection of electrical parts - IP 55; - Sound pressure at 1 m - 68 dBA +/-2; - Amount of distillate with 75% alcohol content in one cycle - 30/160 l; - Amount of processed raw material at a temperature of 100 °C for unloading from distiller in each cycle - 750/880 l; - Last user achieved performance with 12% ABV wine - 85 l/h of product with 95% alcohol content. 3. Installation composition (see diagram A): A - Alcohol discharge device; B - Filter for neutral substances; C - distillation column; D - Flow capacitor; E - Alcohol vapor condenser; F - Distillate cooler; G - Head fraction tank; H - Final fractions tank; I - Radiator; L - Control panel with thermometers.
Specifications
Manufacturer | ,,Cadalpe" |
Model | C27 |
Condition | Used |
Stock Number | 231.2 |